Trends in Commercial Vehicles 2025: Commercial vehicles of tomorrow: more efficient, lighter and safer
06/04/2016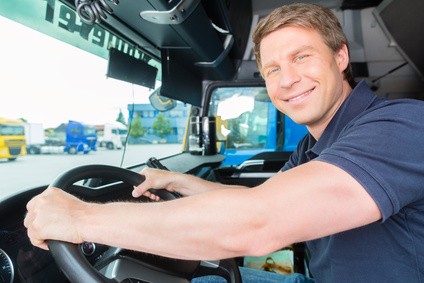
Schlegel und Partner has evaluated upcoming technology trends in commercial vehicles (CV) for the next decade. Three factors could be identified: technologies, efficiency and safety. This article provides a brief overview of measures which can be adopted.
Background:
The drivers of commercial vehicle development differ significantly from those of light vehicles (LV). Key criterion for LVs is initial cost; for CVs, it is the total cost of ownership (TCO) that is decisive. In CV development only those technologies will be introduced which have a payback period of at most four and in some cases only two years from date of purchase. The calculation is typically based on total cost per ton kilometer. And the safety of drivers, passengers and other road users also has an impact on cost, as expenses of non-operation can be avoided. Most other changes typically follow legislative requirements.Powertrain:
Exhaust gas recirculation (EGR) and selective catalytic reduction by aqueous urea solution (SCR) are established measures for emission reduction. The introduction of variable valve timing (VVT) in commercial diesel engines is relatively new. Other key functions may include internal EGR achieved by increased valve-opening overlap as well as improved control of exhaust and catalyst temperature assisted by appropriate fuel injection. Improved control and efficiency of exhaust after-treatment in stop-start operation or coasting mode can also prove beneficial. In the search for additional fuel saving potential, it is worth noting that exhaust heat is responsible for the greatest systemic energy losses of combustion engines. Recovery of this thermal energy offers huge potential for savings (Waste Heat Recovery = WHR). Different technologies can be applied for utilization of this energy. The main focus of development work is currently on the Rankine steam cycle. The objective is to regain the exhaust heat as mechanical work. This can be accomplished either by direct mechanical propulsion support or – as is currently much more likely – by means of a generator which can produce a much more variable supply of electricity to power other electric “consumers”.Due to the high level of power required, some auxiliaries are currently linked mechanically to the engine although peak power is not permanently required. This ineffective energy use can be countered in two ways. First, auxiliaries can be decoupled once they are not needed, which is commonly done, e.g. in the case of A/C compressors. Secondly, an electric drive can be used if sufficient electric energy can be harvested, e.g. by the use of WHR. Then an electric coolant pump can additionally be considered. The loss of efficiency arising from dual energy conversion from mechanical to electric energy and back is more than compensated by the variable operation permitted by the electric auxiliary drive. Other auxiliaries with potential for saving energy through electrification are the hydraulic power steering pump and the air compressor for brakes and suspension.Automated manual transmissions preferably used in heavy duty trucks in most cases do not provide power shift ability. This means that vehicle speed decreases during the course of the gear change operation until the next gear is engaged. This causes a loss of acceleration work. By means of dual clutch transmissions (DCT) even in trucks, these losses can be avoided. DCTs thus contribute to fuel saving and improve acceleration. Consequently, gear steps can be designed wider allowing for a wider gear ratio spread with the same number of gears and enabling a higher total ratio and a lower engine speed, all contributing to fuel efficiency. While WHR is most beneficial for vehicles with almost constant load, as e.g. in long haulage, a hybrid module is most suitable in a transient operating mode. Here, one or two electric machines located parallel to the typical powertrain can support the propulsion or generate electric energy. A smaller engine can be used, as peak power can be provided through electric boost. If the electric propulsion power is high enough, purely electric operation will also be possible, e.g. in urban areas. Electric energy not utilized for propulsion purposes can power new electric auxiliaries. Driver assistance systems:
Not only is efficient operation necessary, but effective vehicle operation also contributes to TCO reduction. Current driver assistance systems support drivers in route selection with minimum congestion delay or in maximizing energy saving by selection of the topographic route profile with lowest energy demand. Aspects of weather such as wind or rain will be considered accordingly. Further technologies can be applied to support driving at constant speed with minimum acceleration or deceleration periods. Among these are platooning, in which a number of tractor-trailers follow a leading truck through a virtual drawbar directed and controlled by the first driver. This enables high safety levels and low fuel consumption. Another area of research not yet evaluated very deeply is the consideration of losses caused by cornering and friction of non-steered wheels. Besides steered axles, the design of new steering devices and consideration of steering losses in navigation will increasingly be considered.General conditions:
The use of gaseous fuels such as natural gas or regeneratively produced gases such as methane offers a huge advantage compared to diesel fuels with regard to emissions as these fuels can be burnt with much lower after-treatment demands. The large fuel tanks then needed make this fuel preferable for city buses or distribution traffic traveling short distances. As a substitute for fossil diesel fuel, biogas-to-liquid fuels (btl fuels) can be applied as they have comparable properties and require few adaptations for conventional diesel engines.The possible legalization of longer tractor-trailer trains may provide further fuel saving potential as may the application of speed sensitive spoilers or further aerodynamic measures, such as use of cameras instead of exterior mirrors, which all enable reduction of fuel consumption through reduced drag.Summary:
All the examples mentioned show that many opportunities exist which may increase the efficiency and effectiveness of commercial vehicles at reduced emissions. Most of them require the application of emission and consumption optimized diesel engines.© Schlegel und Partner 2016Picture: © Kzenon | fotolia.com
The drivers of commercial vehicle development differ significantly from those of light vehicles (LV). Key criterion for LVs is initial cost; for CVs, it is the total cost of ownership (TCO) that is decisive. In CV development only those technologies will be introduced which have a payback period of at most four and in some cases only two years from date of purchase. The calculation is typically based on total cost per ton kilometer. And the safety of drivers, passengers and other road users also has an impact on cost, as expenses of non-operation can be avoided. Most other changes typically follow legislative requirements.Powertrain:
Exhaust gas recirculation (EGR) and selective catalytic reduction by aqueous urea solution (SCR) are established measures for emission reduction. The introduction of variable valve timing (VVT) in commercial diesel engines is relatively new. Other key functions may include internal EGR achieved by increased valve-opening overlap as well as improved control of exhaust and catalyst temperature assisted by appropriate fuel injection. Improved control and efficiency of exhaust after-treatment in stop-start operation or coasting mode can also prove beneficial. In the search for additional fuel saving potential, it is worth noting that exhaust heat is responsible for the greatest systemic energy losses of combustion engines. Recovery of this thermal energy offers huge potential for savings (Waste Heat Recovery = WHR). Different technologies can be applied for utilization of this energy. The main focus of development work is currently on the Rankine steam cycle. The objective is to regain the exhaust heat as mechanical work. This can be accomplished either by direct mechanical propulsion support or – as is currently much more likely – by means of a generator which can produce a much more variable supply of electricity to power other electric “consumers”.Due to the high level of power required, some auxiliaries are currently linked mechanically to the engine although peak power is not permanently required. This ineffective energy use can be countered in two ways. First, auxiliaries can be decoupled once they are not needed, which is commonly done, e.g. in the case of A/C compressors. Secondly, an electric drive can be used if sufficient electric energy can be harvested, e.g. by the use of WHR. Then an electric coolant pump can additionally be considered. The loss of efficiency arising from dual energy conversion from mechanical to electric energy and back is more than compensated by the variable operation permitted by the electric auxiliary drive. Other auxiliaries with potential for saving energy through electrification are the hydraulic power steering pump and the air compressor for brakes and suspension.Automated manual transmissions preferably used in heavy duty trucks in most cases do not provide power shift ability. This means that vehicle speed decreases during the course of the gear change operation until the next gear is engaged. This causes a loss of acceleration work. By means of dual clutch transmissions (DCT) even in trucks, these losses can be avoided. DCTs thus contribute to fuel saving and improve acceleration. Consequently, gear steps can be designed wider allowing for a wider gear ratio spread with the same number of gears and enabling a higher total ratio and a lower engine speed, all contributing to fuel efficiency. While WHR is most beneficial for vehicles with almost constant load, as e.g. in long haulage, a hybrid module is most suitable in a transient operating mode. Here, one or two electric machines located parallel to the typical powertrain can support the propulsion or generate electric energy. A smaller engine can be used, as peak power can be provided through electric boost. If the electric propulsion power is high enough, purely electric operation will also be possible, e.g. in urban areas. Electric energy not utilized for propulsion purposes can power new electric auxiliaries. Driver assistance systems:
Not only is efficient operation necessary, but effective vehicle operation also contributes to TCO reduction. Current driver assistance systems support drivers in route selection with minimum congestion delay or in maximizing energy saving by selection of the topographic route profile with lowest energy demand. Aspects of weather such as wind or rain will be considered accordingly. Further technologies can be applied to support driving at constant speed with minimum acceleration or deceleration periods. Among these are platooning, in which a number of tractor-trailers follow a leading truck through a virtual drawbar directed and controlled by the first driver. This enables high safety levels and low fuel consumption. Another area of research not yet evaluated very deeply is the consideration of losses caused by cornering and friction of non-steered wheels. Besides steered axles, the design of new steering devices and consideration of steering losses in navigation will increasingly be considered.General conditions:
The use of gaseous fuels such as natural gas or regeneratively produced gases such as methane offers a huge advantage compared to diesel fuels with regard to emissions as these fuels can be burnt with much lower after-treatment demands. The large fuel tanks then needed make this fuel preferable for city buses or distribution traffic traveling short distances. As a substitute for fossil diesel fuel, biogas-to-liquid fuels (btl fuels) can be applied as they have comparable properties and require few adaptations for conventional diesel engines.The possible legalization of longer tractor-trailer trains may provide further fuel saving potential as may the application of speed sensitive spoilers or further aerodynamic measures, such as use of cameras instead of exterior mirrors, which all enable reduction of fuel consumption through reduced drag.Summary:
All the examples mentioned show that many opportunities exist which may increase the efficiency and effectiveness of commercial vehicles at reduced emissions. Most of them require the application of emission and consumption optimized diesel engines.© Schlegel und Partner 2016Picture: © Kzenon | fotolia.com