Wind Energy: Almost every new plant is a prototype
02/03/2012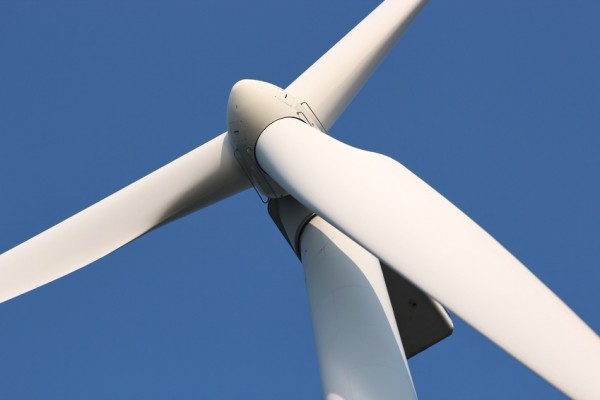
Wind energy generation is rapidly emerging as a resource efficient, low carbon and cost-effective technology around the world. Global nameplate wind power capacity increased from 17 GW in the year 2000 to 159 GW in 2010. Today, existing wind power plants have the capacity to generate about 2.5% of the worldwide electricity consumption. However, not only the total capacity of wind energy plants increased in recent years, but also the size of the individual power units. In addition, the adopted technologies still advance with enormous pace, which is a real challenge to the manufacturers in the wind industry. Schlegel and Partners supports suppliers to this industry by gaining intelligence about today’s technological requirements and future technology trends.
Rapid advancement in wind energy generation technologies – uncertainty for suppliers to the wind energy industryIn recent years, we could observe an amazing development in the wind power industry: The first wind turbines in the 1980s had a nameplate capacity of around 30 kW each, a rotor diameter of about 15 m, the hub height was around 30 m and the production of electricity was around 35,000 kWh per year. Today, a typical wind turbine has a nameplate capacity of 6,000 kW, a rotor diameter of 126 m, a hub height of 135 m and a production of electricity of about 20 M kWh per annum! This means that today the capacity of a typical wind energy plant is 200 times higher than 30 years ago, the rotor diameter increased by factor 8.5 and the energy application increased by the factor 570. Currently, even larger multi-megawatt machines are being designed for future wind farms. For the suppliers to the wind power industry, it is crucial to evaluate the future sizes of wind turbines: Will the increase in turbine sizes carry on in the future, or are we near the end of the line? Furthermore, due to the pace of new developments in wind power generation, there is little experience with the applied load or the durability of single components in currently developed wind turbines. Latest stress analyses show that many components such as rotors, gears, bearings, and seals are exposed to extreme forces. Consequently, the risks for operators of wind energy parks and for component suppliers concerning the life time of parts and systems are immense. Warranty charges, repair and maintenance efforts and therefore the Returns on Investment of wind energy plants over the whole lifetime can be calculated only with a high degree of uncertainty. We can also observe that the technologies used in wind energy generation are still far from the stage of standardization. For instance, there is an ongoing debate about the fundamental lay out design of wind turbines: will future wind power plants be operated with gears, or will gearless approaches be the state of the art in ten years? Additionally, wind energy parks are more and more often constructed offshore. This means that further stresses and strains caused by environmental conditions in offshore areas have to be taken into consideration, e.g. damages by salt water. For newly developed offshore wind parks, the reduction of idle time and the awareness of upcoming damages at an early stage have a crucial impact upon the profitability of these installations. The unique conditions under which offshore wind power plants operate require totally new maintenance concepts, which have more in common with concepts for offshore oil platforms than with traditional maintenance of wind parks onshore. It needs to be assured that an emergency team is available very close to the sites, so that the inspection of sensors of all crucial components can be carried out as well as immediate minor repairs. Another crucial requirement is the ability to cope immediately with larger damages and to replace crucial components within a narrow time frame. Schlegel and Partners screens current requirements and future technology trendsDesigners and assemblers of wind turbines expect from their components suppliers not only to fulfill their current requirements, but also ask them to anticipate the future development of wind power plants and to actively promote innovative solutions. To do this successfully, it is crucial to understand the current developments in the wind power industry and to assess the future of wind turbine technologies. To generate a sound base of knowledge for strategic decisions of its customers, e.g. for the alignment of research and development, Schlegel and Partners continuously screens market requirements and technology trends in the wind power industry. In our studies, we highlight topics like:
- What kind of technical elastomers will be used in the future?
- Are there any opportunities for newly developed elastomer profiles?
- What are the future requirements for components to offshore wind parks?
- How can the performance of fiber reinforcements be improved by the use of special resins and additives?
- Will the trend towards offshore wind parks require totally new service concepts for components suppliers?
- Is there a future for gears in wind turbines, or will gearless layouts be the state of the art in the future?