Truck technology is in transition
22/11/2012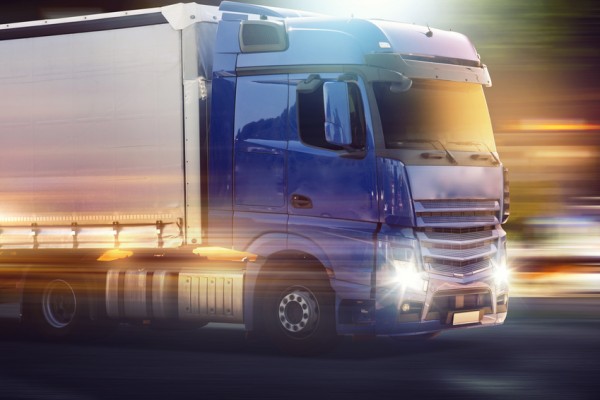
Many advances in heavy commercial vehicles may significantly improve fuel efficiency but require, on the one hand, some five to ten years before implementation. On the other hand, adaptation of road traffic regulations is required to get many of the new improvement technologies on the road.
The development of new heavy truck technology has little in common with the technologies used in passenger cars or light vehicles. Trucks are much heavier, larger and they operate in a much narrower operating range. Trucks are not built for joy rides: they are operated to earn money. This significantly affects the design principles as most design criteria follow the primate of efficiency.Even driver comfort is determined in compliance this criterion. However this does not lead to narrow uncomfortable boxes with lots of handles and levers surrounding the driver’s seat. In contrast, easy handling man-machine interfaces and well-designed interiors create a practical, easy handling workplace with comfort attributes even attracting an ambitious, experienced, and highly skilled workforce with a low accident probability.The main purpose of a truck, i.e. to transport heavy or bulky freight at the highest permitted speed and the lowest possible cost, has immediate design consequences.The turbocharged diesel engines in modern trucks provide full engine torque at a constant level almost from idling over the first two thirds of the engine’s speed range.To minimize fuel consumption engines have to run in their most efficient operating ranges. This requires transmissions with a wide ratio spread meeting power demand at cruising speed on level roads. For maximum efficiency fast shifting is as essential as it is for Formula One cars because each disruption of power throughput leads to reduced acceleration and lower average speed. In addition it increases fuel consumption which means additional cost.Whereas in the past automated transmissions selected transmission ratios in accordance with current load, today’s dual clutch transmissions enable shifting without loss of traction, anticipate topographic gradients by use of GPS mapping, and utilize momentum in ascending the next peak.Whereas reduced engine speed also reduces friction inside the engine, further measures were undertaken to reduce friction in auxiliaries by variabilizing their function. This concerns, e.g., water pumps, compressors, hydraulic steering pumps, and wheel bearings and seals, to mention just a few.While passenger cars show an aesthetic teardrop design enabling low coefficients of drag, trucks and trailers necessarily have a box design with sharp edges and corners. Nevertheless, research has led to design measures significantly reducing drag. These include spoilers and NACA nozzles at the back end of the trailer, air intake shutters, cabin side, roof, and floor spoilers, and trailer side panels. Modification of length specifications is required to permit fast introduction of these measures without incurring loss of cargo space.Many of these design and drag-reducing measures create additional weight which is often unacceptable for trucks carrying heavy loads such as coils or tank and dump trucks. To offset the additional weight or to create a competitive advantage, lightweight design is a permanent objective. Axles were reduced in weight by up to half a ton and practically all components have been subjected to a rigorous design diet. Consequently, curb weight has shrunk and load capacity risen. Under real life conditions optimized trucks today consume only one liter of fuel per 100 ton km. Trailer and axle designs in carbon fiber demonstrate what is technically feasible whereas optimized steel and aluminum combinations provide affordable low weight solutions.Thinking beyond the restrictions imposed by current federal road traffic regulations, a significant increase in efficiency ensues on operating, e.g., two trailers with one tractor. Field projects in Europe are under way and will probably show how to further reduce emissions while ensuring full functionality.New technologies with mid- or long-term implications focus on regenerative braking systems. Today wheel brakes, engine brakes, and retarders provide deceleration by transforming kinetic energy into heat energy. This energy is typically passed on to the environment by heat exchangers. Application of the hybrid technologies increasingly used in passenger cars permit utilization of the deceleration energy of speed-adaptation braking or a fraction of downhill braking to generate electricity which is stored in supercaps or Li-ion batteries. This energy may operate electrically driven auxiliaries such as air compressors, A/C, cabin consumers, or lighting, thus reducing engine load to save diesel fuel. Savings up to 15% are feasible.Thermal energy recovery systems employ either an expansion machine or thermoelectric processes to utilize exhaust heat. Fuel consumption can be reduced by up to ten percent in this way.We learn that short and long term measures will significantly improve specific fuel consumption per ton kilometer but require modification of existing road traffic regulations by government to transform these brilliant engineering ideas into reality.